Les câbles électriques sous-marins ne sont pas nouveaux et existent depuis plus d’un siècle. Au début, ils servaient à approvisionner les phares et les navires.
Les améliorations récentes des procédés de fabrication de câbles, la technologie de conversion de puissance et les méthodes d’installation de câbles ont connu une augmentation de leur utilisation pour les projets de transmission de puissance. Les applications modernes incluent l’alimentation électrique des îles, la connexion de réseaux autonomes, les parcs éoliens offshore, l’alimentation de plates-formes marines et les traversées à courte distance pour transporter l’électricité à travers les rivières, les canaux ou les baies.
Le dimensionnement des câbles sous-marins modernes est similaire à celui des câbles terrestres, avec seulement quelques nuances. Certaines différences importantes qui affectent le courant nominal résident dans les domaines de la construction des câbles et des conditions d’installation. Le courant nominal final pour tout chemin de câble doit être basé sur les conditions les plus contraignantes. Par conséquent, plusieurs calculs sont souvent nécessaires pour un seul et même projet.
1. La composition des câbles sous-marins de puissance
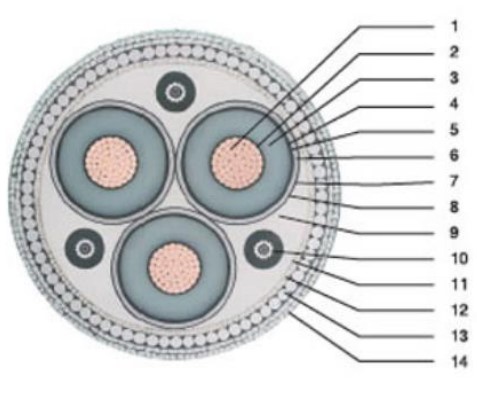
- 1 – Conducteur en cuivre toronné, scellé longitudinalement
2 – Couche extrudée semi-conductrice
3 – Composé d’isolation XLPE (conception sèche)
4 – Couche extrudée semi-conductrice
5 – Barrière longitudinale semi-conductrice contre la pénétration d’eau
6 – Ruban longitudinal cuivre/aluminium ou alliage de plomb
7 – Colle de liaison ou soudure ou couche anti-corrosion
8 – Gaine polyéthylène
9 – Mastic
10 – Câble interstitiel fibre optique – la disposition des 52 fibres optiques : 1 groupe de 48 conducteurs pour la communication et le contrôle, 2 groupes de 2 conducteurs (1 conducteur pour la détection de température et 1 noyau pour la détection des dommages
11 – Ruban de liaison
12 – Literie en polypropylène
13 – Armure en fils d’acier galvanisé
14– Couche en polypropylène.
-
1.1. Les Conducteurs
1.1. Les Conducteurs
Les conducteurs des câbles sous-marins sont normalement en cuivre toronné car il a une meilleure conductivité et une meilleure résistance à la corrosion que l’aluminium. Notez cependant que certains projets de câbles sous-marins consistent à la fois en cuivre et en certaines sections de conducteurs en aluminium et que plusieurs calculs de puissance de câble peuvent être nécessaires.
Les tronçons du câble peuvent être de tailles non standard. Les câbles sous-marins ne sont normalement pas achetés sur étagère et donc les tronçons du câble, plutôt que d’être construites selon des valeurs standard (c’est-à-dire celles de la norme CEI 60228), sont conçues pour répondre aux besoins d’un projet en particulier avec ses spécificités et ses exigences. Par exemple, des tailles de conducteur non standard de 790 et 1410 mm2 ont été utilisées et jusqu’à 3500 mm2 sont fabriqués.
Le choix du matériau conducteur (cuivre ou aluminium) est basé sur les considérations suivantes :
Conductivité électrique : Une conductivité plus élevée conduit à une taille de conducteur plus petite pour la même capacité de transport de courant. Des conducteurs plus petits entraînent l’utilisation de moins de matériau pour les autres couches de câble telles que l’isolation, l’écran, la gaine ou les fils d’armure. Une taille de câble plus petite entraîne également une augmentation de la longueur de câble qui peut être supportée par le navire d’installation.
Résistance mécanique et flexibilité : Les câbles sous-marins doivent être capables de résister physiquement aux forces mécaniques lors de l’installation et de l’exploitation. Les conducteurs en cuivre ont une résistance mécanique plus élevée que les conducteurs en aluminium.
Résistance à la corrosion : La corrosion est un problème important pour les installations de câbles électriques dans les environnements sous-marins. Le cuivre a une meilleure résistance à la corrosion que l’aluminium.
Des agents gonflants sont utilisés entre les couches conductrices pour assurer l’étanchéité à l’eau et éviter la pénétration d’eau lors d’un défaut.
Considérations de poids : Le poids des câbles eux-mêmes a un impact sur la force de tension mécanique exercée sur les câbles au niveau de l’enrouleur du tambour du navire, qui peut être excessive.
Le poids de l’aluminium pur est d’environ 1/3 de celui du cuivre pur. Par conséquent, pour une même surface de conducteur, le poids de l’aluminium est bien inférieur à celui du cuivre. Cependant, le courant nominal des conducteurs en aluminium est inférieur à celui du cuivre.
En général, pour les câbles haute tension, la différence de poids entre un câble avec des conducteurs en aluminium ou un câble avec des conducteurs en cuivre est minime pour la même capacité de transport de puissance.
-
1.2. L’Écran du conducteur
1.2. L’Écran du conducteur
L’écran du conducteur est constitué d’une couche de matériau semi-conducteur qui contient du carbone noir et qui est extrudée sur le conducteur et utilisée pour lisser l’intensité du champ électrique pendant le fonctionnement entre les rainures, les crêtes et les creux du conducteur et l’isolant.
Pour déterminer les courants nominaux, l’épaisseur de la couche d’écran du conducteur et sa résistivité thermique doivent être prises en compte dans les calculs.
-
1.3. L’Isolant (l’isolation thermodurcissable)
1.3. L’Isolant (l’isolation thermodurcissable)
L’isolant des câbles sous-marins n’est pas différent de celui des câbles terrestres. L’isolation en XLPE est le premier choix pour les câbles sous-marins AC ou DC. Le caoutchouc XLPE ou EPR est parfois utilisé pour les câbles MT pour les applications sous-marines. L’isolation en EPR a de meilleures performances à l’arborescence d’eau (water-treeing) par rapport au XLPE mais a des pertes diélectriques plus élevées.
-
1.4. La Gaine métallique (bloquant l’eau)
1.4. La Gaine métallique (bloquant l’eau)
Les gaines métalliques sont couramment utilisées dans les câbles sous-marins pour agir comme une barrière radiale contre l’eau et peuvent également agir comme un écran métallique. Pour les câbles sous-marins à trois conducteurs, les gaines sont généralement autour de chacun des noyaux conducteurs.
Une gaine est utilisée pour protéger contre la pénétration d’eau dans l’isolant. La gaine peut être fabriquée en utilisant une variété de matériaux, y compris l’aluminium, le plomb ou le cuivre dans une variété de formes. Les gaines en cuivre sont utilisées là où la flexion continue ou la flexion des câbles est endurée. Dans les câbles sous-marins moyenne tension, une gaine polymère en combinaison avec un agent absorbant l’humidité peut être utilisée à la place pour économiser sur les coûts.
Le type de gaine métallique de loin le plus couramment utilisé consiste en une gaine en alliage de plomb extrudée recouverte d’une gaine polymère extrudée ou de bandes semi-conductrices qui offre une protection contre la corrosion ainsi qu’une protection mécanique pour les gaines de plomb souples. Une alternative aux gaines de plomb extrudées sont des rubans soudés en cuivre ou en aluminium, mais si l’aluminium est utilisé, une certaine forme d’anode sacrificielle est nécessaire pour protéger de la corrosion.
Notez qu’il est de pratique courante que les câbles de réseau sous-marin à trois conducteurs MT pour les parcs éoliens offshore ne nécessitent pas de gaines métalliques bloquant l’eau, seuls les câbles d’exportation HVAC le font.
L’étanchéité longitudinale, qui empêche la migration de l’eau le long de l’intérieur du câble après un dommage mécanique, est généralement réalisée à l’aide de poudres, de rubans ou de fils gonflables sous la gaine métallique.
-
1.5. L’Armure
1.5. L’Armure
L’armure est très importante dans la construction de câbles sous-marins et remplit de nombreuses fonctions importantes, notamment en fournissant une résistance statique et dynamique pendant l’installation ainsi qu’une protection mécanique pendant le fonctionnement.
Des pertes de circulation dans les câbles sous-marins AC en raison du blindage nécessaire sont à prendre en compte. La présence d’une armure se traduira par d’importantes pertes de courant circulant à l’intérieur du câble qui réduiront le courant nominal. Aucune perte ne se produit dans l’armure des câbles sous-marins HVDC.
Une astuce pour réduire les pertes d’armure pour les câbles sous-marins AC est d’installer un conducteur de retour en cuivre qui fonctionne pour réduire considérablement ou pour annuler complètement les pertes d’armure dues au courant induit qui circule dans la direction opposée au conducteur provoquant un champ magnétique contre-actif /flux.
Il existe de nombreux types possibles de matériaux et de constructions d’armures. L’armure en fil d’acier inoxydable, bien que coûteuse, est considérée comme idéale car elle est amagnétique à faible perte, offre une bonne protection mécanique en raison de sa haute résistance et a une bonne résistance à la corrosion par l’eau de mer. La grande majorité des câbles électriques sous-marins utilisent des fils d’acier galvanisé qui sont enroulés en hélice autour du câble.
Il peut y avoir une seule couche d’armure ou des constructions de câble d’armure à double couche utilisées. Des câbles blindés à double couche sont généralement utilisés pour les extrémités des circuits pour une résistance à la tension mécanique supplémentaire.
-
1.6. La Couche extérieure
1.6. La Couche extérieure
Une couche externe protectrice est utilisée consistant en une gaine en plastique ou plus communément en fil de polypropylène (souvent multicolore pour une haute visibilité dans les environnements sous-marins) qui s’enroule étroitement autour des couches d’armure, ce qui permet d’éviter la mise en cage des fils d’armure lors de l’installation.
2. Les conditions d’installation
Il est important d’avoir une connaissance détaillée des conditions d’installation et de l’environnement thermique d’un câble. Une connaissance précise de ces paramètres tout au long du parcours du câble permet d’économiser sur l’investissement initial, d’améliorer la fiabilité et d’augmenter la durée de vie du câble.
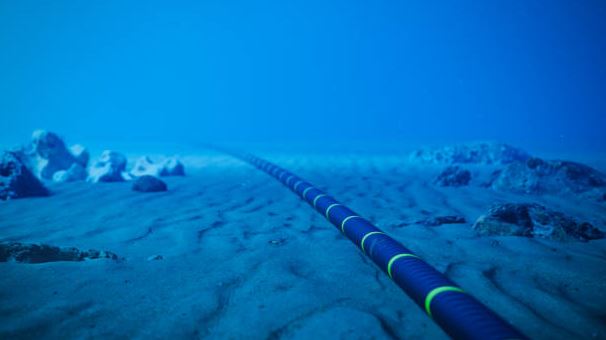
-
2.1. La Profondeur d’enfouissement
2.1. La Profondeur d’enfouissement
Les câbles électriques sous-marins sont généralement enterrés entre 1 et 3 m sous le niveau du fond marin. Les câbles sont normalement installés à l’aide d’une charrue à câble qui est remorquée depuis un navire.
-
2.2. La Résistivité thermique des sols sous-marins
2.2. La Résistivité thermique des sols sous-marins
Les sols sous-marins ont généralement une résistivité thermique relativement faible de 1 C.w/W ou moins.
La résistivité thermique des sols dépend du matériau de base du sol, de la densité sèche, de la distribution de la taille des grains, du compactage, de la teneur en humidité et de la teneur en matières organiques.
La résistivité thermique des sols sous-marins ne varie pas beaucoup et en raison de sa saturation en eau, la résistivité thermique est assez faible.
Le tableau ci-contre indique la résistivité thermique supposée pour les types de sols sous-marins courants.
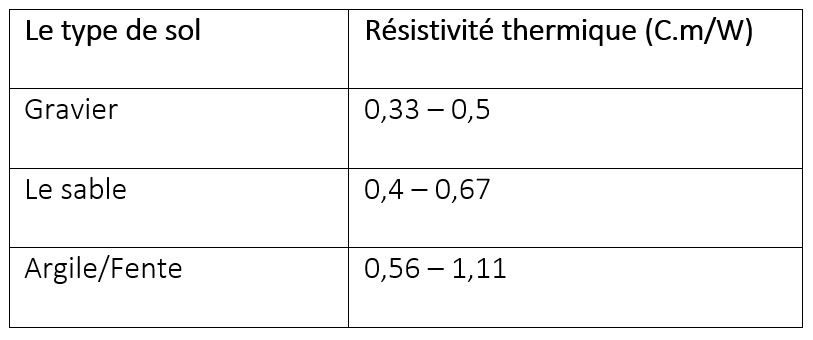
Il est très important d’avoir des échantillons réels et suffisants de sols sous-marins pour un projet le long du parcours d’installation. En effet, il peut y avoir des sections de sol contenant une teneur élevée en matière organique et celles-ci ont une résistivité thermique beaucoup plus élevée.
-
2.3. La Température ambiante
2.3. La Température ambiante
La température ambiante d’un câble est définie comme la température au lieu du câble si le câble n’y était pas. La température ambiante est une valeur critique dans tous les calculs de courant nominal, quelles que soient les conditions d’installation utilisées ou les cas de charge considérés.
Pour les câbles sous-marins non enfouis, il s’agit simplement de la température de l’eau du fond marin, qui est généralement inférieure et plus constante que la température à des niveaux d’eau moins profonds, mais en fait elle varie considérablement au cours de l’année ou sur plusieurs années. Normalement, la température la plus élevée du fond marin sur une période de 10 ans ou plus est utilisée dans le dimensionnement d’un câble sous-marin.
Pour les câbles sous-marins enterrés, la température ambiante à la profondeur d’enfouissement réelle peut être considérée, qui est inférieure à la température du fond marin. Cette valeur peut être calculée à l’aide d’un logiciel métier.
3. Le calcul de courant nominal
Il existe plusieurs méthodes de calcul acceptables pour effectuer les calculs d’intensité nominale, y compris des méthodes analytiques telles que celles de la CEI 60287 (évaluations en régime permanent) ou de la CEI 60853 (pour les évaluations dynamiques), des méthodes numériques telles que la méthode des éléments finis ou des méthodes hybrides.
Les conditions d’installation peuvent varier considérablement le long du parcours du câble sous-marin. Les sections du tracé du câble qui sont les plus susceptibles d’être thermiquement restrictives comprennent :
- Lorsque les câbles sont acheminés à travers des murs de défense contre la mer à l’intérieur de conduites ou de tunnels.
- Les tubes en I ou en J de la sous-station offshore ou des plates-formes des éoliennes.
- À travers des sols sous-marins à très haute résistivité thermique (généralement à forte teneur en matière organique).
- À proximité de sources de chaleur provenant d’autres câbles électriques ou de canalisations chauffées.
Il n’est souvent pas économique de dimensionner les câbles électriques sous-marins en fonction des sections les plus onéreuses du tracé du câble. Par conséquent, la taille du conducteur ne peut être augmentée que pour les sections courtes où il y a des « points chauds » grâce à l’utilisation de jonctions. Parfois, la majorité du parcours du câble peut utiliser un câble conducteur en aluminium, tandis que des conducteurs en cuivre sont utilisés pour les sections critiques.
Bien que le calcul des courants nominaux pour les câbles électriques sous-marins présente des similitudes avec celui des câbles terrestres, il nécessite une attention particulière.
La formule suivante (CEI 60287-1-1) est généralement utilisée pour dimensionner un câble sous-marin en courant.

A Ynni Consulting, nous utilisons des logiciels de calculs numériques dédiés pour apporter plus de précision à nos calculs de dimensionnement.
Vous voulez savoir comment nous pouvons vous aider ?
Références :
- CEI 60287-3-1 : 2017 Câbles électriques – Calcul du courant nominal.
- CIGRE FT 610, « Raccordement des câbles de production offshore », 2015.
- CIGRE FT 640, « Un guide pour les calculs de calibre des câbles isolés », 2015.
- Electrical Power Systems Design & Analysis Software ELEK Articles.